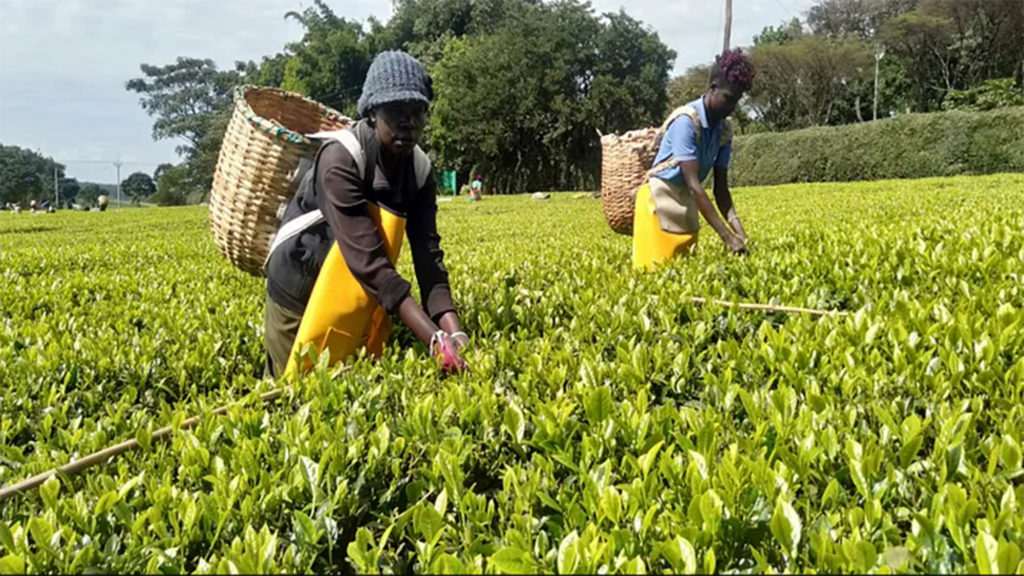
The Institute for Manufacturing (IfM), part of the University’s Department of Engineering, has partnered with top Kenyan tea exporter Eastern Produce Kenya (EPK) to promote simple and effective energy-saving practices at two of their tea estates in Nandi Hills.
Kenya is one of the world’s biggest producers of tea, employing over 600,000 smallholder farmers, which support over three million people. But drying, grading and packaging mean tea production is highly energy intensive.
In 2020, EPK invited IfM to apply the ‘Cambridge Sustainable Continuous Improvement Method’ (developed at the IfM’s Centre for Industrial Sustainability) to help re-focus their efforts on reducing the amount of energy used at their tea factories.
The Cambridge Method is eight simple steps that can be implemented over 12 months to deliver sustainability improvement with minimal investment. By looking at factory data, the method identifies the key drivers of the factory and then helps the factory to pick the areas where sustainability aligns with business success.
Through online meetings and workshops, IfM worked with EPK to identify where energy could be saved and how to make sustainability relevant and understood by the factory workers. After just 12 months, teams reported a 15-30% reduction in thermal and electric energy consumption at both sites. There was also a significant increase in tea produced per unit of fuel wood (kWh/m3).
Some of the straightforward actions included improving firewood storage by expanding covered wood storage areas. Steam usage was also reduced by eliminating steam leaks and cleaning dust from radiators and heat exchangers. And to reduce electricity, the team were encouraged to switch off lights and sockets and using natural lighting instead.
One of the key success factors was getting the local team engaged in the changes and making the sustainability gains relevant to their context. This was done by converting energy into something recognisable: ‘how many cows can you buy with the savings?’ By the end of the project, the team worked out that they had saved 2,000 cows – the size of the President’s herd. By engaging the local workforce, making sustainability relevant and identifying simple steps that significantly reduce energy consumption, the ‘Cambridge Method’ is now being used at five EPK sites in the Nandi Hills.
“Since working with IfM, everything we implemented has been continued. Shop floor workers now own the energy-saving culture. Some team members have now moved to other factories and are implementing these ideas in these factories. So, the ideas and what we have learnt are spreading. We’re working together effectively and committed to bringing our customers tea that has a minimal impact on the environment.”
– Chris Ballard, EPK Technical Director